
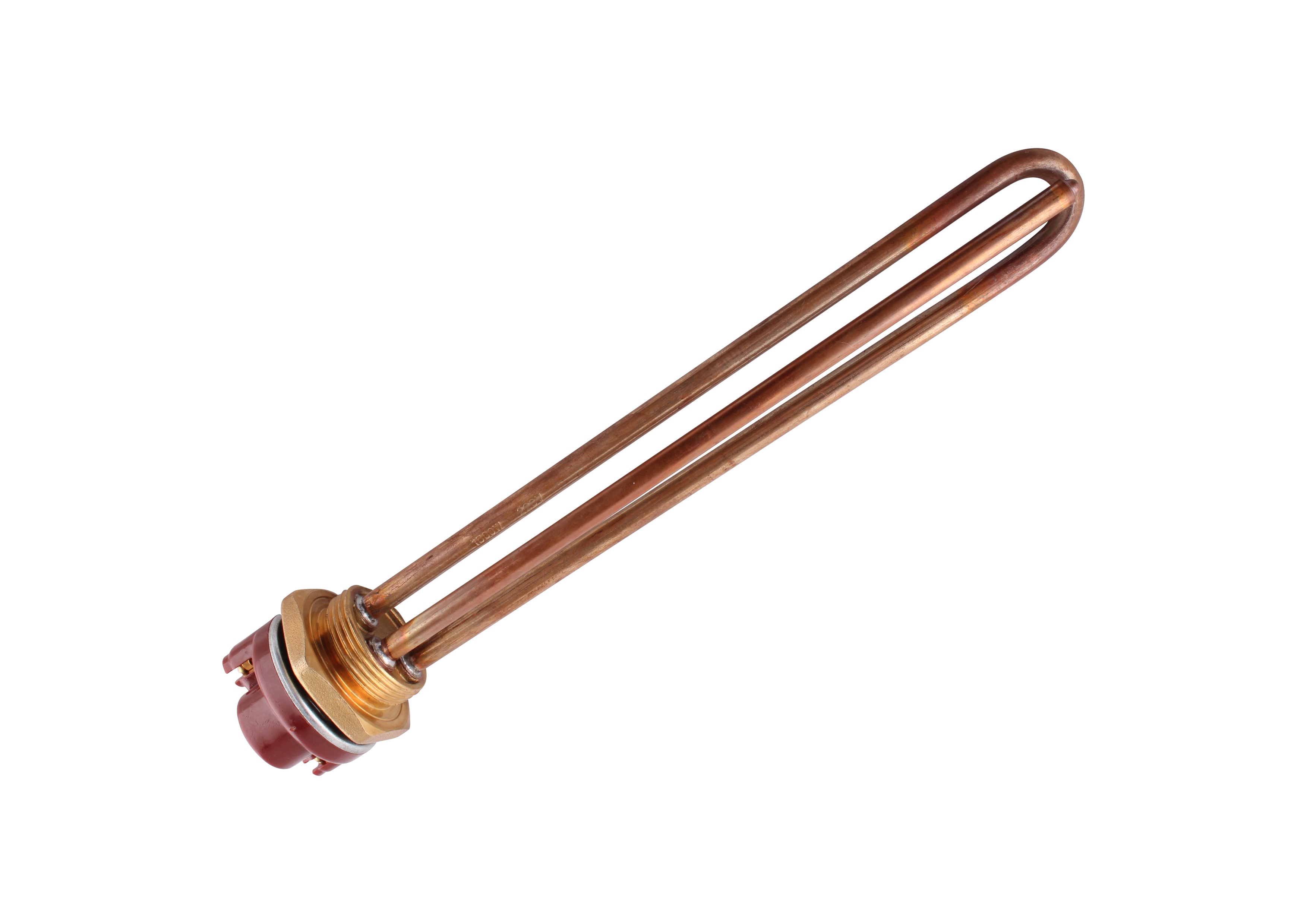
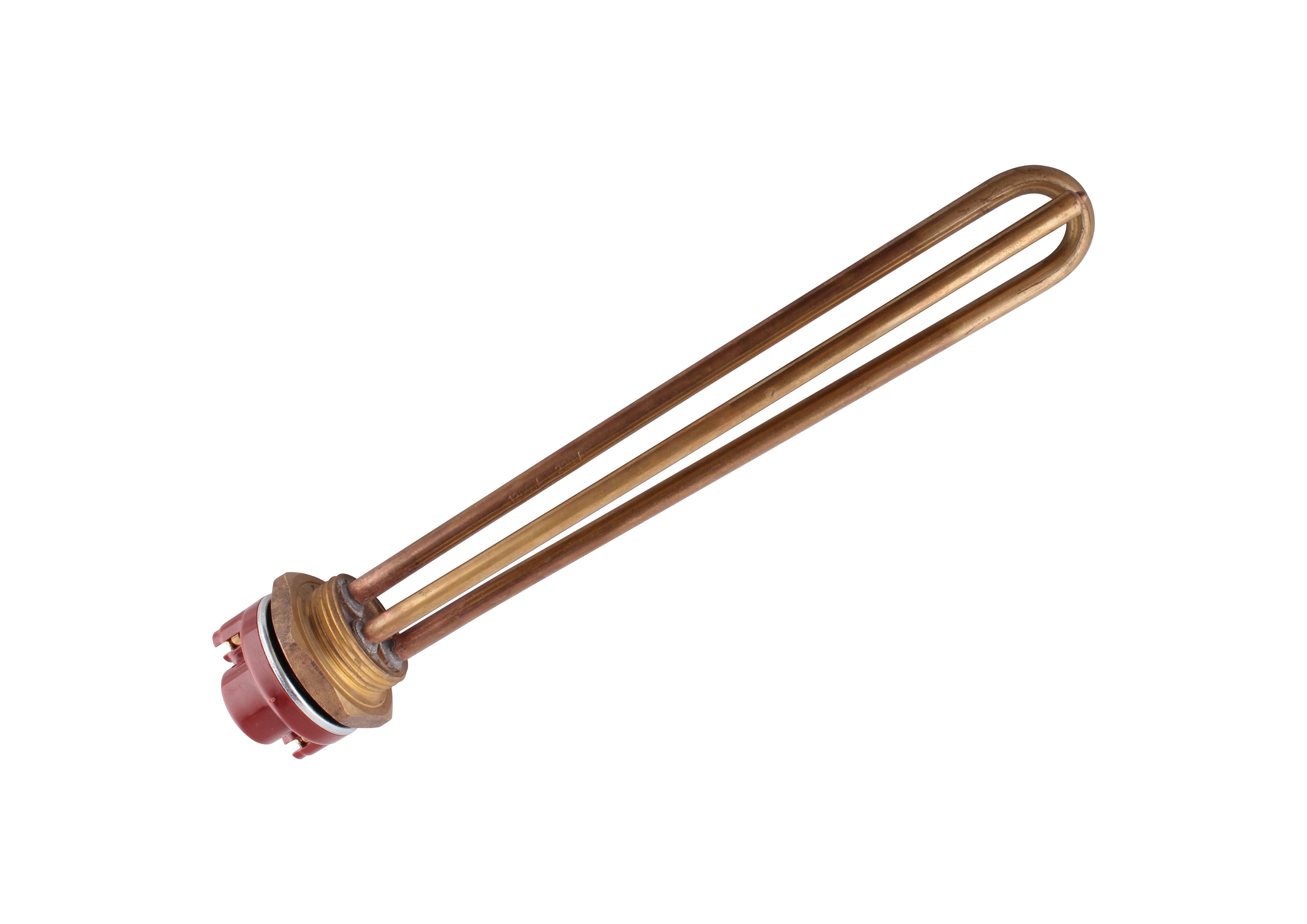
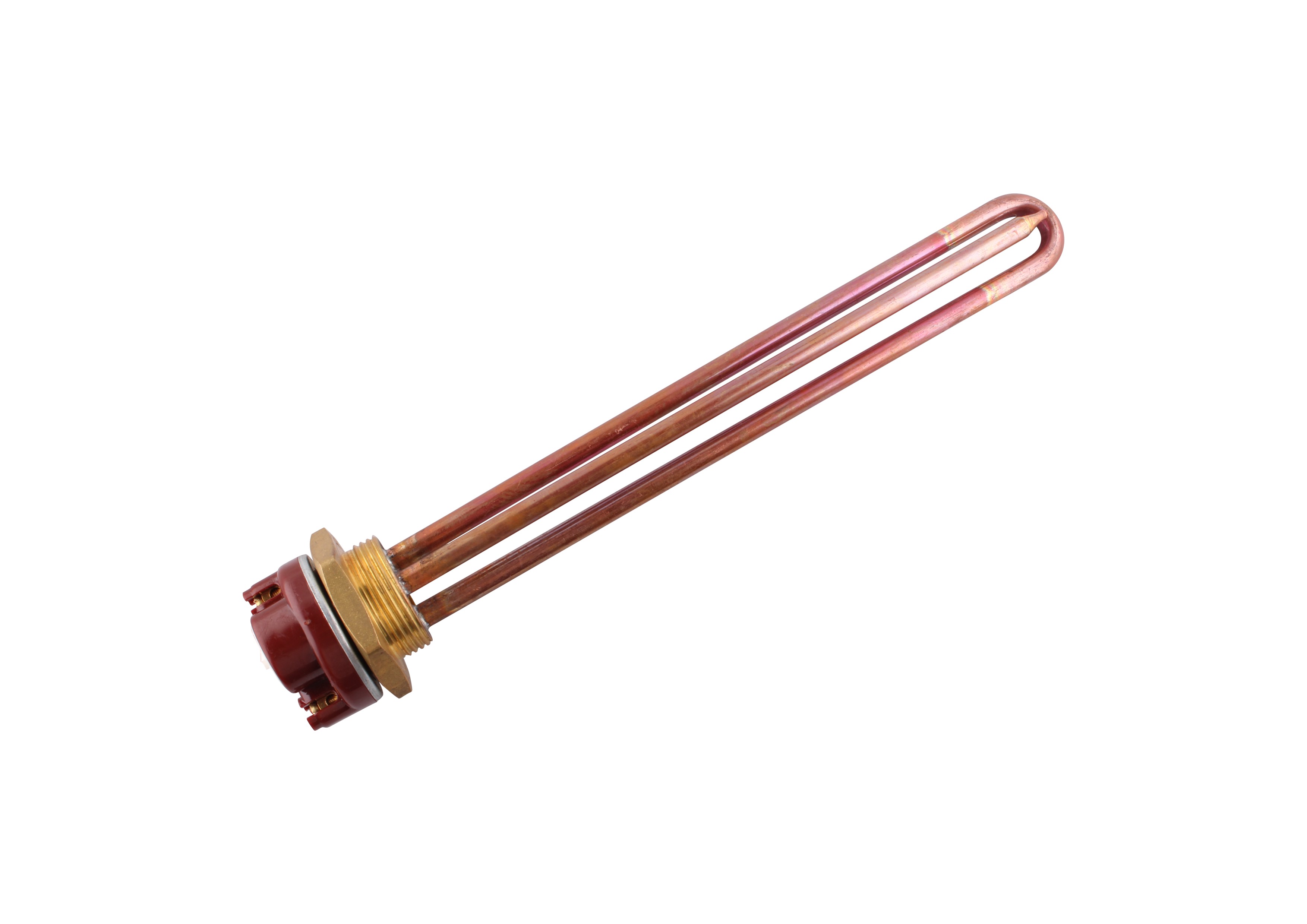
Why choose copper material to create high-performance electric heating tube
Among the many materials that can be used to make electric heating tubes, copper stands out for its excellent thermal conductivity. As a metal element with excellent ductility and chemical stability, copper can not only conduct heat quickly and evenly, but also maintain long-term stable operation in a variety of harsh environments. It is one of the preferred core raw materials for industrial heating equipment.
Compared with stainless steel or nickel alloys, copper not only has a higher thermal conductivity, but also exhibits good oxidation resistance at high temperatures. This makes it particularly suitable for thermostatic control systems in continuous production environments, greatly reducing the burden of post-maintenance frequency and replacement costs.
The science behind high-density heating
behind every high-efficiency copper electric heating tube is inseparable from the support of precision design. The internal nested resistance wire generates Joule effect through current excitation, and relies on the tightly packed magnesium oxide layer to achieve insulation protection while accelerating the energy transfer process. This mechanism determines the accuracy of the temperature control of the entire system.
In addition, it is worth noting that as the purity of raw materials increases, the overall work efficiency also increases significantly. Therefore, we always insist on using high quality electrolytic copper as the basic raw material source, only to bring you a more durable and energy-saving product experience.
Design points and market positioning of high-power heating rods
For applications that require extremely high heating rates, it is clear that traditional standard models cannot meet the increasing operating needs. To this end, a series of high-power heating rod series products designed for high-strength loads have been specially developed and launched, which have shown strong adaptability and superior performance in both chemical reaction kettle and mold preheating process.
In order to meet the diverse demands of various customers, we have carried out in-depth optimization and improvement work in multiple dimensions such as shape size, interface style, and power adjustment range. The new generation of modular design concept bred from this has greatly improved the universal compatibility level of the product, allowing users to freely combine and match the most suitable configuration scheme according to the actual situation.
Future Development Trend of Intelligent Temperature Control System Enabling
Imagine if you can remotely control the status changes of all related devices with a touch of the screen. Is the picture already in your mind? This is a new door opened for us by the coming era of intelligence. With the new temperature control device supported by the latest sensing technology, you can grasp the working conditions of each key node at any time and make timely response and adjustment measures.
At the same time, the closed-loop feedback system based on the IoT network architecture also helps to further extend the life of the whole machine. Through continuous collection and analysis of operating data to predict the location of potential failures and hidden dangers, preventive measures are taken in advance to truly achieve the ideal state of worry-free operation and maintenance.
The application and expansion of dry-burning heat pipe: from laboratory to production line
Tracing back to the origin of the first batch of professionals dedicated to the study of efficient heat transfer in the dry state, mainly concentrated in universities and research institutes. After numerous repeated tests and verifications, it was finally confirmed that this type of device can indeed maintain exceptionally excellent heat exchange efficiency without the intervention of liquid media, which prompted the latecomers to gradually introduce it into commercial applications and be widely used.
Now we can be pleased to see that this advanced technology has been widely adopted in many industrial chains. Whether it is the instantaneous sterilization equipment required for the food and beverage sterilization assembly line, or the die heat preservation unit indispensable in the extrusion molding process of plastic products; Even the aging test of the power battery pack of electric vehicles is indispensable.
Under the pressure of the harsh and changeable actual operating environment, the only way out is to continuously improve the product quality level and service guarantee level. In this regard, we are also actively improving the existing sealing structure design scheme, strengthening the strength index value of the shell protective coating and other measures to promote the implementation process, and strive to provide users with a more secure and reliable ultimate heating solution.
Conclusion: Whether you are a business owner who pursues extreme efficiency or a purchasing manager who pays attention to cost-effective advantages, please believe that only brand manufacturers who truly understand the nature of customer needs can tailor the most suitable exclusive product for you. Let us join hands to meet the upcoming wave of technological innovation impact baptism!
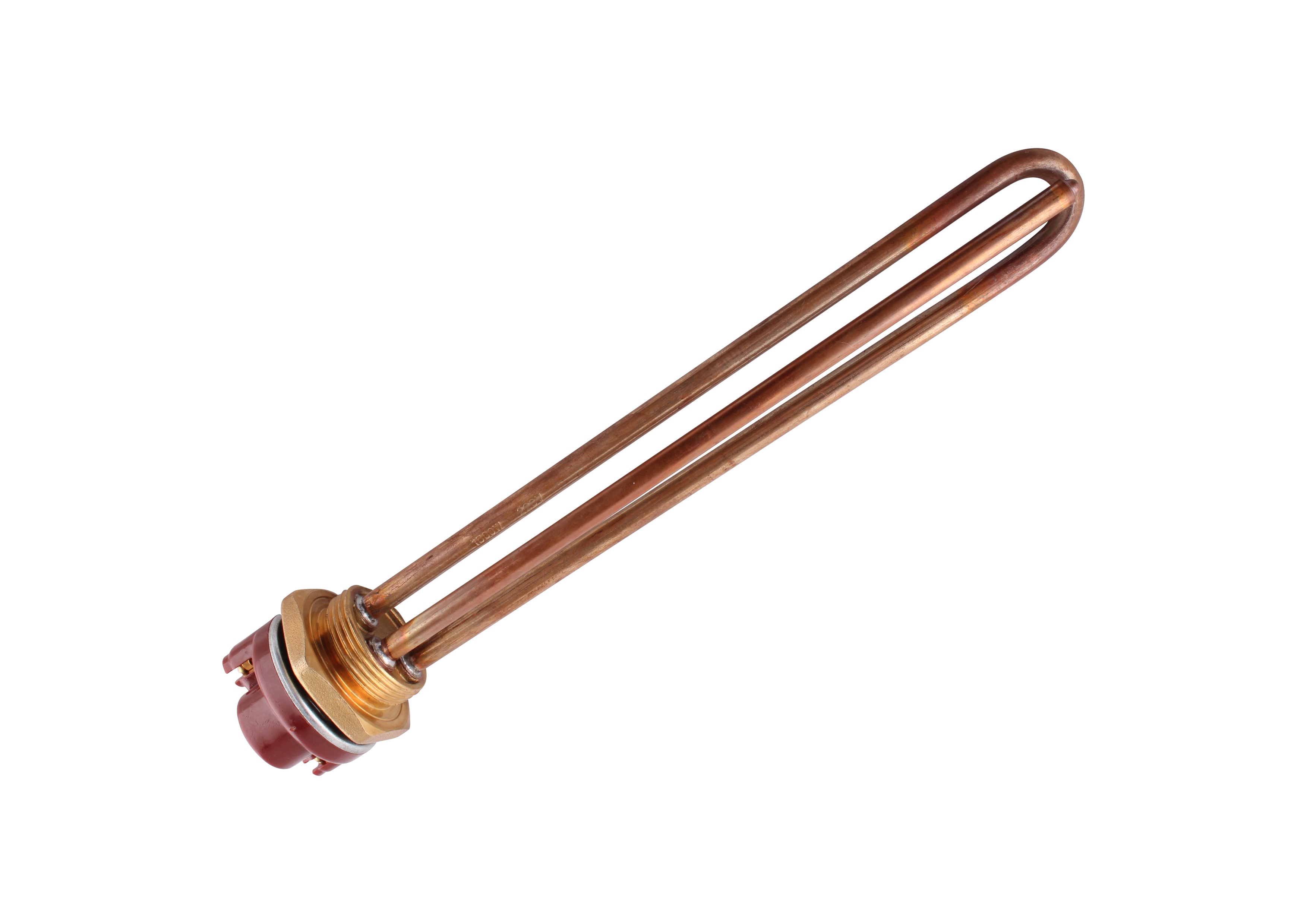